A cold chain update
The importance of the cold chain for the pharmaceutical sector cannot be overstated.
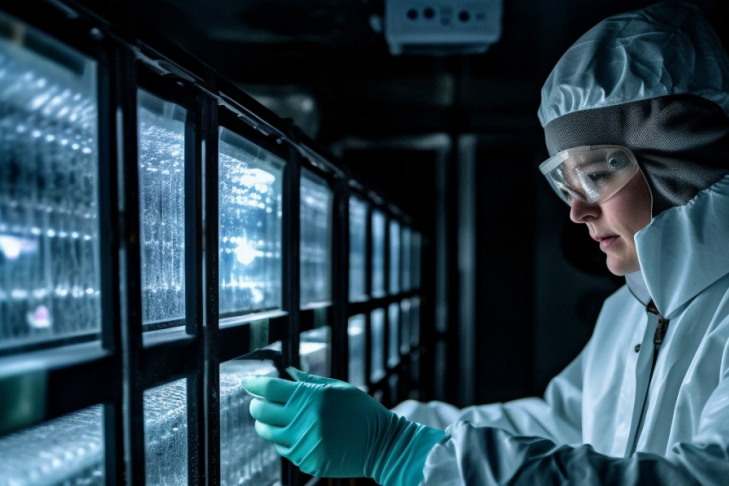
Indeed, it is a vital component of the modern pharmaceutical ecosystem. Its importance has become emphasized even further during the last couple of years because of the Covid pandemic, with many vaccines needing to be produced, manufactured, delivered, and stored in temperatures as low as minus 80 degrees Celsius. These vaccines have joined a host of other lifesaving, and life-improving products which rely on a low-temperature environment throughout all stages of their life cycle.
While vital to the successful operation of the pharmaceutical sector, a watertight cold chain is also important to other industries, notably food, especially frozen and chilled produce.
Let’s take this opportunity to remind ourselves the rationale behind the growing importance of the cold chain and look at how it is driving change throughout the pharmaceutical sector.
A rapidly expanding pharmaceutical cold chain
Cold chain logistics accounted for more than 26% of the pharmaceutical industry in 2019, an already substantial share that is steadily increasing.
When you consider the fact that pharma revenues worldwide came to a total of 1.48 trillion U.S. dollars in 2022, you begin to see just how important the cold chain currently is – and it is set to become even more essential in years to come.
Why is the cold chain so important?
Some medicines, drugs, and vaccines need to be continuously stored in a limited temperature range from the time they are manufactured until the moment of vaccination. This is because temperatures that are too high or too low can cause the vaccine to lose its potency or its ability to protect against disease.
Once a vaccine loses its potency, it cannot be regained or restored. It is, therefore, vital to ensure these products are kept at the correct temperature at all stages of its life cycle. If the potency is lost, not only will the pharmaceutical provider have to destroy and re-manufacture the product, which will come at a very steep cost, many people could potentially be at risk of disease or even death if they are urgently waiting for the vaccine.
Such cold-chain pharmaceutical products include modern biologic therapeutics, such as monoclonal antibodies and vaccines, cellular and gene therapies, certain types of insulin, and some cancer treatments. And, recently, we have been introduced to the temperature-sensitive Covid vaccines, which were researched, developed, produced, and delivered across the world in ultra-rapid time.
In fact, as our list of common and not-so-common health problems grows, so do our expectations for cures and treatments. And the pharmaceutical industry is rising to the challenge by providing us with an ever-wider array of pharmaceuticals, many of them requiring temperature-controlled transportation under proper cold chain management.
Consider for one moment the complexity of delivering temperature-sensitive vaccines. It takes a chain of precisely coordinated events in temperature-controlled environments to store, manage and transport these products. Just one fluctuation in temperature at any one point of the supply chain could result in the collapse of the supply chain and ultimately result in a batch of useless vaccines.
Governments and regulatory authorities across the world are increasingly recognising the importance of ensuring this never happens. They are taking solid steps to introduce mandatory regulations that must always be adhered to, rules that will benefit the population as a whole, plus help to protect the bottom line of those manufacturing the products.
The cold chain and regulation
As is the case with much of the pharmaceutical sector, cold chain operations are subject to rigorous regulatory processes. In recent years, there’s been a clear shift towards standardising global transportation regulations for healthcare-related products.
In the USA, the Food and Drug Administration (FDA) sets out its standards for the manufacture, storage, and distribution of pharmaceutical and food products in the Current Good Manufacturing Practices (CGMP). It covers all the steps in the supply chain, from transport operations, labelling and packaging to personnel training and record-keeping.
Likewise, the EU has published the Good Distribution Practice of Medicinal Products for Human Use (GDP). The aim of compliance is to maintain the quality and the integrity of medicinal products. Like its USA equivalent, it covers aspects such as quality management systems, personnel, premises and equipment, documentation, and qualification of suppliers and customers.
Governments are not the only organisations introducing regulations. The International Air Transport Association (IATA) sets out its standards for transporting pharmaceutical products by air in its comprehensive Temperature Control Regulations (TCR). It also requires a Time and Temperature Sensitive Label to be affixed to all shipments booked as time and temperature sensitive cargo.
Furthermore, since 2013, airlines and ground-handling agents must use IATA’s Standard Acceptance Checklist for time and temperature-sensitive shipments to ensure that essential control activities are carried out.
The effect of regulating every step, from manufacture all the way through to dispensing, to prevent cross-contamination, product degradation, and even the infiltration of counterfeit products, is encouraging logistic companies to specialise in shipping pharmaceuticals, medical devices and healthcare-related products. These companies have a detailed understanding of the regulatory and logistical requirements of shipping such products door-to-door, helping manufacturers guarantee quality and efficacy.
The cold chain, serialization, and the future
The successful implementation of the pharmaceutical cold chain has three main components – production and packaging, transport and storage, and an efficient roll out involving fully trained personnel. It is essential that all three of these elements work in unison.
We are already seeing some major changes stemming from an increased cold chain adoption. One of the major changes is a complete overhaul of existing packaging and serialization solutions. Established systems in operation until relatively recently simply could not cope with harsh temperatures of up to minus 80 degrees Celsius. The advent of Covid, and the resulting vaccines that needed to be kept at such low temperatures meant that a full set of hardware and software had to be designed, manufactured, and implemented ultra-quickly.
This technology continues to evolve. One of the big developments we continue to see is around mobile technology for the supply chain. We are seeing a much more coordinated approach to being able to log events with mobile devices. We will also be able to directly link specific supply-chain events to vaccine outcomes.
We are also continuing to see an increased usage of barcoding, helping to reduce errors in dispensing in stressful periods. Should the world be unfortunate enough to experience another pandemic, vaccines and test kits developed to detect the virus will need to continue to be supplied across the world quickly and efficiently – which requires more standardization.
We will also see an even more increased reliance on business intelligence. This will be used to ensure an even swifter and more efficient vaccine serialization process. Intelligence will be used to assess exposure times, optimize routing, and scan exceptions, all while being able to monitor and measure continuously.
In addition to this, a much higher emphasis on human safety and comfort now needs to be factored in. The harsh temperatures in a cold chain environment mean workers need adequate protective equipment and regular breaks, with limitations to the number of hours they can spend in cold conditions.
Additionally, we have seen a whole host of “extras” launched to facilitate the production, storage, and delivery of cold chain products. Just one example of this is the temperature monitoring device, which is built into the thermal shipping containers, resulting in the need for a new, much more delicate way of opening these containers to prevent damage.
Implementing new technologies
Technology is set to be one of the main drivers of the future cold chain, especially an increased use of robotics.
Well-designed robots will keep working in the harsh temperatures needed – there is no need for them to have regular rest breaks wear insulated clothing or cryogenic gloves, which will be one of the changes we will see applied to human workers. Therefore, we will see companies turning more and more to robots to effectively streamline and automate what were previously manual operations to maintain a steady workflow. Indeed, Gartner predicts that 75% of large enterprises will have adopted some form of smart robots in their warehouse operations by 2026 as they search for flexible automation.
Combine this with colder chains, and we are much more likely to be working alongside robotic colleagues soon.
In conclusion
The cold chain is rapidly rising in prominence as a core component of the pharmaceutical sector across the globe. Modern medicine production and distribution is demanding the cold chain, and governments and regulatory bodies are recognising the importance of the cold chain.
Indeed, we at advanco cite cold chain operations as one of the most important aspects of the wider pharmaceutical sector over the coming years. We need to be aware of the latest developments and ensure we remain at the cutting edge of all that is needed for this important part of the sector.
Without a cold chain, the outlook of tomorrow’s pharmaceutical sector will be bleak. We will therefore keep researching, analysing, planning, and developing to ensure that our pharma serialization solutions perfectly complement the cold chain of the future.
VIEW THE ORIGINAL ARTICLE HERE