Solution for temperature sensitive products
A supply chain that is strictly regulated in terms of temperature has become a vital part of the modern international pharmaceutical ecosystem.
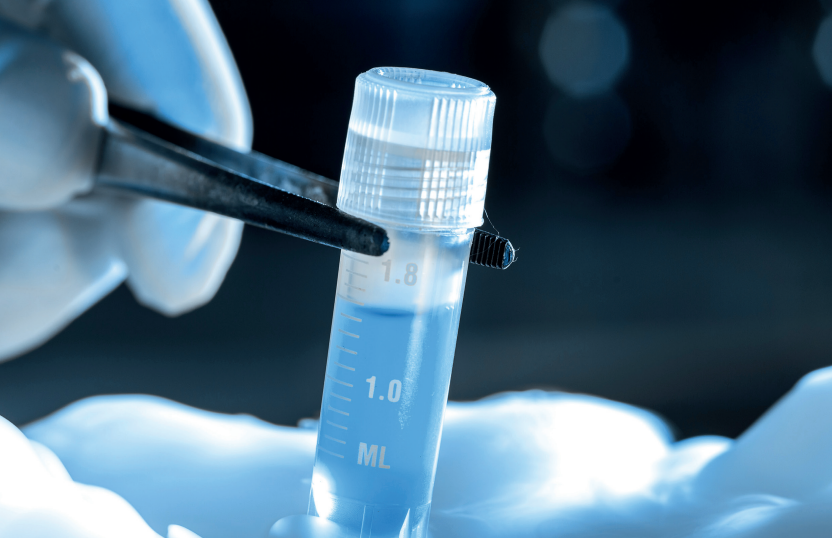
Indeed, various global regulatory requirements shows how entrenched it has now become. For example, the EU has launched its Good Distribution Practice of Medicinal Products for Human Use (GDP). The USA’s Food and Drug Administration (FDA) also sets out its standards for the manufacture, storage, and distribution of pharmaceutical and food products in the Current Good Manufacturing Practices (CGMP).
Therefore, let’s review some recent developments for temperature sensitive product serialization. We will also examine how advanco is leading the way when it comes to implementing the serialization solutions needed for a powerful cold chain.
Why is pharmaceutical cold chain serialization now so important?
Some pharmaceutical products need to be continuously stored in a controlled temperature environment from the time they are manufactured until the moment of vaccination. This is because temperatures that are too high or too low can cause the medicines to lose potency, or the ability to protect against disease.
Once a vaccine loses its potency, it cannot be regained or restored. Indeed, the entire point of the drug can be compromised, making it inefficient or, at the worst-case scenario, making it dangerous for human consumption. It is therefore vital to ensure these products are kept at the correct temperature, at all stages of the life cycle. If the product fails, not only will the pharmaceutical provider have to destroy and re-manufacture it, which will come at a very steep cost, many people could potentially be at risk of disease, or even death.
It is therefore vital to have serialization solutions that are capable of being fully deployed in extreme temperatures – something that was dramatically highlighted during the recent Covid pandemic. This is where advanco’s ARC Cold Chain really comes into its own. It perfectly blends its specialist pre-existing serialization solutions with cutting-edge functions designed especially for the cold chain.
How does advanco’s Cold Chain thrive as a core component of the pharmaceutical sub-zero serialization process?
Some products demand incredibly low temperatures throughout their entire life cycles, temperatures which can be as harsh as minus 80°C. Many previously established systems, technology and machinery simply could not cope with these harsh conditions. This meant that for the case of the Covid pandemic, a full re-design of hardware and software had to be rolled out, manufactured, and implemented at breakneck speed after the pharmaceutical industry was forced to rethink their entire supply chain processes.
The evolution is continuing every day. One of the big developments we continue to see is around mobile technology for the supply-chain. We are seeing a much more coordinated approach to being able to log events with mobile devices. We will also be able to directly-link specific supply-chain events to vaccine outcomes.
We are also seeing an increased usage of barcoding helping to reduce errors in dispensing in stressful periods. Should the globe be unlucky enough to experience another pandemic, vaccines and test-kits developed to detect the virus will need to continue to be supplied across the world quickly and efficiently – which require more standardization.
Advanco’s pharmaceutical cold chain track and trace incorporates all these approaches. It is designed to overcome operational time constraints from packaging to shipping, while always maintaining safety and compliance standards. Advanco’s ARC Cold Chain allows pharmaceutical manufacturers to increase operational efficiency through automation, quickly detect product temperature violations and automatically detect all relevant data from key areas such as refrigerated trucks and cooling rooms – all while maintaining essential compliance and safety standards.
The role of the cold chain temperature monitoring system during the shipping process
Once the pharmaceutical product leaves the temperature-controlled warehouse, it needs to travel in the same very specific conditions, which can involve incredible logistical complexities.
Indeed, the shipping process is arguably the riskiest element of temperature-regulated production. While factories and storage facilities can usually be easily controlled, the transportation part, which could involve shipping and road transport across hot areas of the globe, can be difficult.
We are therefore seeing new cold chain monitoring methods quickly springing up and being adopted as the norm. As an example, some Covid vaccines are shipped in an insulated thermal shipping container with dry ice to keep the vaccine frozen at ultra-low temperatures from minus 80°C to minus 30°C. Because of this, it is important to regularly monitor the temperature of the vaccine at the start and end of each working day. If storing in an ultra-low temperature (ULT) freezer, standard freezer, or thermal shipper, temperatures must be recorded using a freezer temperature form. If storing the vaccine in a refrigerator prior to use, use the refrigerator temperature form.
Cold chain track and trace systems – safety first!
Working in, or even taking delivery of materials that have been produced in cold chain environments, carries with it a higher risk of injury for staff members, so care must be taken.
However, for most pharmaceutical firms, safety is a given, and staff dealing with such conditions will be likely to be provided with all necessary equipment. What is equally as important is ensuring the medications are produced, stored and shipped correctly, all within the regulated temperatures needed. This is the overriding aim – and will be the factor that saves lives for consumers and increases efficiency for the manufacturers.
Cold chain serialization technology – a perfect role for robots
One of the main changes we are likely to see as the evolution of the cold chain continues is the introduction of new technology, such as intelligent sensors and temperature monitoring smart systems.
We will also see an increased use of robotics. Well-designed robots will keep working in the harsh temperatures needed – there is no need for them to have regular rest breaks, wear insulated clothing or cryogenic gloves. Therefore, we will see companies turning more and more to robots to effectively streamline and automate what were previously manual operations to maintain a steady workflow.
Indeed, Gartner predicts that 75% of large enterprises will have adopted some form of smart robots in their warehouse operations by 2026 as they search for flexible automation.
Get in touch!
For a full demonstration of advanco’s Cold Chain, or to request more information, please contact us.